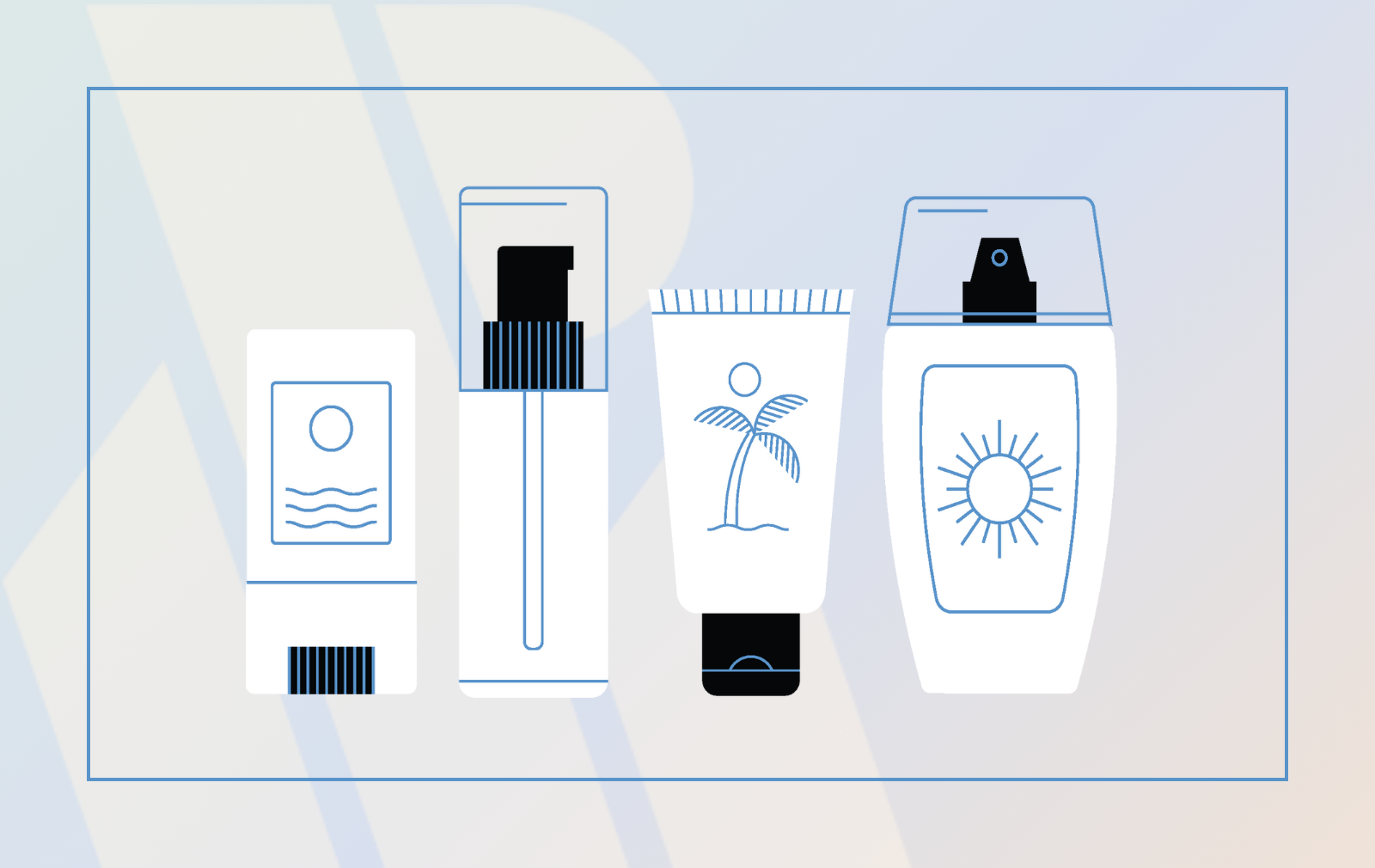
With consumers increasingly becoming aware of the importance of sunscreen in their beauty routines, the category has been booming post-COVID and is projected to grow by 4% each year until 2028. Brands are following the trend by expanding into the sun care category, incorporating SPF into their products, or developing their own sunscreens for customers to add to their routines. Brands new to the SPF process should be aware that the process differs from developing cosmetic products, or even other OTC products, due to regulations, sensitive ingredients and required testing procedures.
In the US, sunscreen is classified as OTC (over-the-counter) drug and must comply with the OTC monograph established by the FDA. (Learn more about The Difference Between Cosmetics and OTC.) The monograph defines the acceptable active ingredients and their concentrations, labeling requirements, and testing standards for sunscreens. Compliance is crucial so it’s important to find a partner that understands the regulatory landscape and can ensure you comply through every step of the process.
READY-FOR-MARKET FORMULAS
Brands can take several approaches when developing a sunscreen: custom development, meaning developing the formula and taking it through the required testing process; private label or white label, which is when the brand chooses an existing formula or product that has already been tested; or Ready-for-Market, which consists of formulas that have already been tested but can be further customized by the brand. Whether it's speed-to-market with a customized Ready-for-Market product or innovation with a custom developed formula, our team can help brands assess and deliver a SPF product that best fits their business needs.
THE SUNSCREEN PRODUCTION PROCESS

R&D: Developing the sunscreen formula
The R&D process begins with a brief to capture the client’s specifications and requirements for the new formula. This guides the R&D chemist on everything from ingredients to include/exclude, texture, benefits, claims, fragrance, format, etc. From this brief, the chemist will build a sample for the client to test and provide feedback on. The chemist will then evaluate the formula and modify based on the feedback until the client approves the sample.
Components: Securing appropriate packaging
Once final approval is given, brand partners will need to identify the components that will be used for the product so that it can be tested in the intended container. Sunscreen products are usually dispensed from containers that minimize air and sunlight exposure, such as tubes, pumps, or airless dispensers to help maintain the integrity and efficacy of the product. Opaque or UV-resistant packaging for sunscreens is important because many sunscreen active ingredients are sensitive to light and heat, especially UV radiation, which can cause them to degrade and become less effective. Exposure to air can also lead to oxidation of some ingredients in the formula, especially for sunscreens that contain organic or chemical UV filters.

Testing: Ensuring safety of product and accuracy of claims
Timeline: 6 months to 1 year
SPF claims are tightly regulated so testing must be conducted according to the FDA guidelines outlined in the monograph to determine the SPF rating. In addition to the SPF testing, which can begin once final approval is given for the product sample, there are a series of tests the product must go through:
PET (Preservative Efficacy Test)
Timeline: 8 weeks
PET is a laboratory test used to assess the effectiveness of preservatives in cosmetic and personal care products in preventing microbial contamination per USP guidelines. The test involves introducing a specified concentration of five different strains of microorganisms into the product. Samples are then taken at specific intervals after inoculation to assess the microbial load within the product. The collected samples are analyzed to determine the effectiveness of the preservative based on the reduction of the initial microbial count or whether no increase occurred from the initial calculated count during the period of the study.
RIPT (Human Repeat Insult Patch Test)
Timeline: 8 weeks
RIPT is a standard dermatological test used to assess the potential for skin irritation or sensitization caused by cosmetic and personal care products. The test involves recruiting a group of human subjects with different skin types. The product being tested is applied to small patches or areas of the skin on the subjects' backs. After the specified duration, the patches are removed, and the test sites are assessed for signs of skin irritation, such as redness, swelling, itching, or other skin reactions. The process is then repeated with multiple applications to help determine if skin irritation or sensitization occurs with continued use.
Stability Study
Timeline: 6 - 12 months
6 months of completed accelerated study = 2-years of exp date
12 months of completed accelerated study = 3-years of exp date
The OTC stability test evaluates various aspects of a product's stability product over its entire shelf life, which can range from several months to several years. The test assesses how a product's physical, chemical, and sensory attributes change over an extended periods of time and under different storage conditions. These conditions are designed to accelerate potential product degradation, allowing researchers to evaluate product stability over time. The tests are conducted both in a glass jar and the product’s components.
The samples are tested at various time points to cover the product's entire shelf life. Various parameters are assessed at each time point, including physical characteristics, chemical stability, microbial testing, and packaging integrity. Researchers collect data and measurements at each time point and record any changes or deviations from the product's initial characteristics, which are then analyzed to determine whether the product remains within acceptable quality standards.
FDA SPF Value Testing
Timeline: 3 weeks
In addition to standard safety tests required for cosmetics or OTC products, sunscreens will be tested to determine SPF Value, which can begin once final approval is given for the product sample. SPF testing in the US is conducted according to specific FDA guidelines and procedures to ensure that SPF claims on product labels accurately reflect the level of protection provided. SPF testing is typically conducted at specialized testing facilities which have controlled environmental conditions to ensure consistent and accurate results.
The SPF test involves human subjects who are willing to have sunscreen applied to their skin. The sunscreen product is applied to a small, defined areas of the subjects' skin and exposed to the UV radiation, while adjacent areas are left untreated as controls. A specific amount of sunscreen is applied per unit area of skin. A controlled source of UV radiation which emits UVB and UVA radiation is used to simulate sunlight exposure and mimic real-world conditions. The test areas with sunscreen and the control areas without sunscreen are then exposed to UV radiation for a specified period. The SPF is calculated by comparing the amount of UV radiation required to produce a minimal erythema dose (MED) on the sunscreen-treated skin with the amount required on the untreated control skin. The SPF is determined by dividing the MED for the sunscreen-treated skin by the MED for the control skin. Multiple subjects and test sites are typically used to obtain statistically significant results. The data collected is analyzed to ensure accuracy and reliability.
SPF value testing can be performed to determine either the static SPF value or the water-resistant SPF value (after 40 minutes or after 80 minutes). To determine the water-resistant SPF value, the procedure is the same as described above, except that the SPF value measurements are performed after applying the sunscreen and after immersion of the subject in water for specified periods of time. Testing performed under these conditions supports a “water resistant” claim for a product.
FDA Broad Spectrum Testing
FDA’s broad spectrum test procedure is designed to determine whether a sunscreen product provides adequate protection against both UVA and UVB radiation, making it eligible for a "Broad Spectrum" claim on its label. It is and in-vitro test that involves measuring the UV absorbance of sunscreen product via a spectrometer to calculate the critical wavelength. Controlled sources emit UV radiation across a range of wavelengths. Based on the spectral absorbance, the critical wavelength is calculated. A mean critical wavelength of 370 nm or greater is classified as broad-spectrum protection.

Production: From PO to delivery
PO
Once the product passes all tests to ensure the product’s formula and components are safe for consumers, a PO (Purchase Order) can be placed, and the product is moved into the production phase of the cycle.
Procurement
The next step in the process involves procuring all the elements needed for manufacturing the product including the components, master box, artwork, and raw materials. A bulk of the production timeline involves procuring the elements needed for production and can be dependent on a variety of factors like location of supplier, availability, world events, etc. After all these elements are delivered to the manufacturer, quality assurance and product planning can begin.
Quality Control and Production
Quality assurance inspection involves systematic and thorough examination and evaluation of products, materials, or processes to ensure they meet predetermined quality standards and specifications. A QC team member will inspect all incoming raw materials, components, or parts to ensure they meet quality standards. At the same time, preparation will begin for production, involving planning how a product will be manufactured to make the process as efficient as possible.
Once a plan is made for production and all components and raw materials are cleared, production can be scheduled. Quality control will also perform batch testing and quality checks during and after manufacturing and packaging to verify product consistency and adherence to specifications. After production is complete and the final product is signed off by quality assurance, the product can be delivered to the brand partner’s specified location for storing or distribution.
READY-FOR-MARKET FORMULAS
Due to the OTC drug classification of sunscreens and the need to ensure safe and accurate sun protection, the timeline for bringing a newly developed sunscreen to market can be longer than a typical cosmetic product by up to one year. One approach that brands can take to avoid the extended timeline is to opt for a Ready-for-Market formula. Ready-for-Market formulas are formulas that have already been developed and tested to substantially shorten your product development timeline and bypass the additional 6-months to 1-year testing period required for the OTC R&D Stability Study. Formulas may also be further customized so that your product aligns with your brand and target audience. This can be a great solution for brands looking for speed-to-market add quality sunscreens to their product lines.
We understand that the process of bringing a sunscreen concept to market can be complex, especially for brands that are new to the category. Our team of project managers have the experience to expertly guide your brand each step of the way. Reach out to your Prime Matter Labs project manager for more info on sunscreen development and our collection of pre-developed Ready-for-Market formulas at help@primematterlabs.com or start your project here.